Achieving GMP and Manufacturing Excellence: Driving Efficiency While Maintaining Compliance
1/26/20258 min read
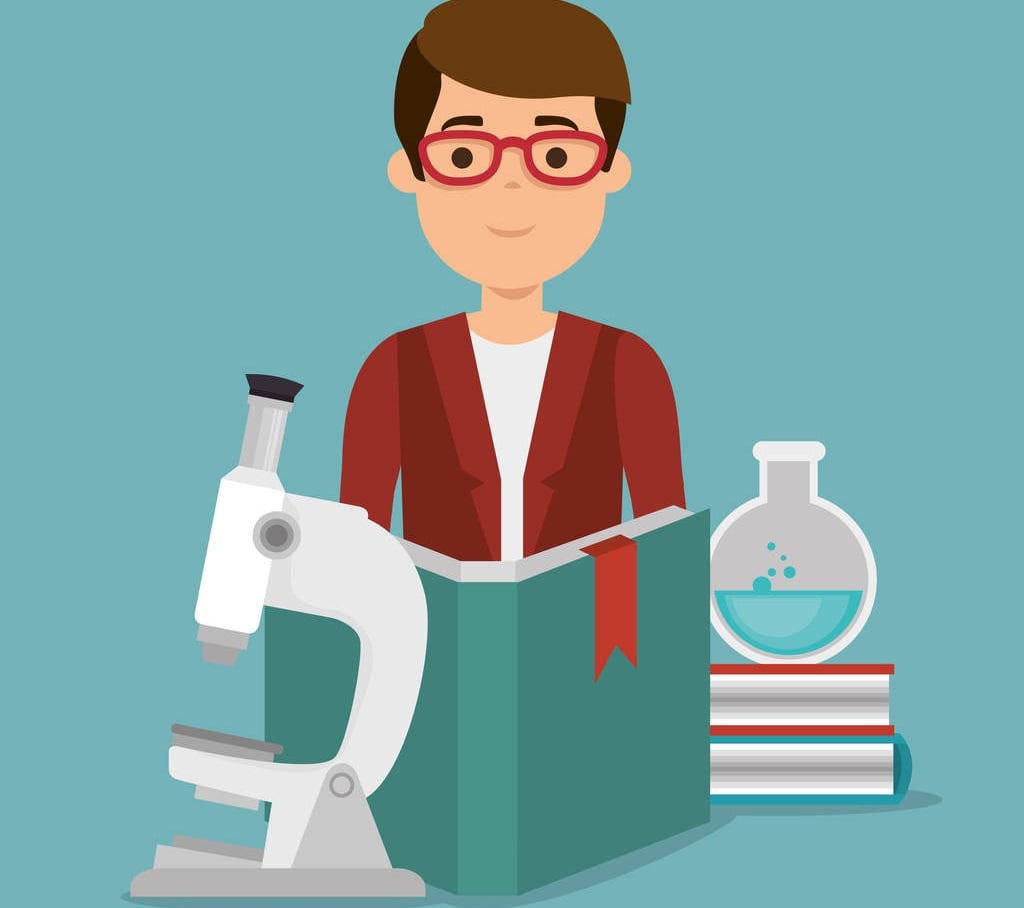
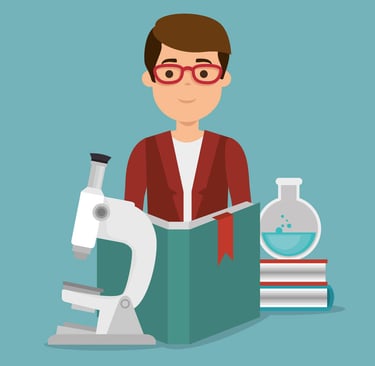
Understanding GMP and Its Importance in Manufacturing
Good Manufacturing Practices (GMP) serve as a vital framework for ensuring the quality and safety of products, particularly within the pharmaceutical and manufacturing sectors. GMP guidelines, which are enforced by regulatory bodies such as the Food and Drug Administration (FDA) and the European Medicines Agency (EMA), establish standardized procedures that manufacturers are required to follow. These guidelines are designed to minimize risks involved in production that may negatively impact product quality, thus ensuring consumer safety.
The importance of GMP compliance cannot be overstated, as it directly affects the reliability and integrity of the manufacturing processes. Regulatory authorities actively monitor compliance with GMP guidelines through inspections and audits. Failure to adhere to these regulations may result in severe consequences, including product recalls, legal penalties, and, in extreme cases, the closure of manufacturing facilities. Hence, manufacturers must not only understand and implement GMP principles but also continuously audit their processes to maintain compliance.
Integrating GMP into manufacturing processes yields numerous benefits that extend beyond mere compliance. By adhering to GMP, manufacturers enhance operational efficiency and reduce wastage, as a systematic approach often leads to improved quality control and consistent product outcomes. Furthermore, GMP fosters a culture of safety and accountability within organizations, which can lead to heightened employee morale and satisfaction. In an increasingly competitive marketplace, tech-savvy manufacturers recognize that robust GMP practices can serve as a differentiating factor, gaining consumer trust and loyalty.
In summary, Good Manufacturing Practices are a foundational element that not only ensures the safety and quality of products but also drives consistency and efficiency in production. By prioritizing GMP compliance, manufacturers can position themselves for long-term success while safeguarding public health and adhering to regulatory standards.
GMP Audit Checklists: Ensuring Facility, Equipment, and Personnel Compliance
In the realm of Good Manufacturing Practice (GMP), audit checklists serve as essential tools for ensuring compliance across various operational dimensions, including facility, equipment, and personnel. These checklists provide a structured approach to evaluating adherence to regulatory standards, thereby facilitating ongoing operational excellence. The components of an effective GMP audit checklist typically encompass predefined criteria that focus on critical areas of compliance.
Facilities must be regularly assessed to guarantee that they meet the stringent cleanliness and environmental controls required by GMP regulations. The checklist should include components such as access control, cleanliness protocols, and maintenance records. Additionally, the layout of the facility should promote efficient workflows and minimize cross-contamination risks. Ensuring that all aspects of facility maintenance align with GMP standards is vital for maintaining product quality and safeguarding public health.
When it comes to equipment, the checklist should encompass aspects such as calibration, maintenance history, and validation documentation. Regular audits ensure that equipment is operating efficiently and is compliant with applicable regulations. Adequate documentation is necessary to verify that equipment is routinely serviced, and it plays a critical role in the risk management strategies mandated by GMP guidelines.
Moreover, personnel compliance is equally significant. Audit checklists should include assessments of training records, competency evaluations, and adherence to hygiene practices. Continuous training ensures that staff are knowledgeable about current GMP standards and their role in maintaining compliance. Regular reviews of personnel qualifications contribute to a skilled workforce capable of driving operational effectiveness.
The importance of regular audits cannot be overstated, as they not only help in identifying potential compliance gaps but also reinforce a culture of continuous improvement. By developing comprehensive GMP audit checklists, companies can better prepare for audits, ensuring that every critical compliance aspect is addressed and operational efficiency is achieved consistently.
Tech Transfer Frameworks: Risk Assessments and Process Validation Templates
Tech transfer frameworks play a pivotal role in the pharmaceutical and biotechnology sectors, particularly during the transition from development to manufacturing. A structured approach ensures that all operational processes adhere to regulatory compliance while maintaining high operational efficiency. Central to this framework are risk assessments and process validation templates, which facilitate a thorough evaluation of each step in the tech transfer process.
During the tech transfer process, organizations must navigate various stages, including planning, execution, and evaluation. Each of these phases presents unique challenges that necessitate meticulous attention. Risk assessments are critical to identifying potential risks associated with each stage and adopting proactive measures to mitigate them. By employing systematic methodologies, organizations can analyze the likelihood of risks, assess their potential impact, and prioritize them based on severity. This type of analysis is not only valuable for compliance but also enhances overall efficiency by preventing disruptive setbacks.
In parallel, process validation templates serve as essential tools in standardizing the validation activities throughout the tech transfer continuum. These templates provide a cohesive structure, ensuring that all necessary parameters are evaluated comprehensively. They facilitate the documentation of results, streamline the review process, and assist in meeting regulatory requirements. By implementing effective process validation strategies, organizations can ensure that manufacturing practices are consistently replicable, thereby alleviating concerns related to product quality and compliance.
Moreover, the combination of rigorous risk assessments and robust process validation templates leads to improved decision-making and fosters a culture of continuous improvement. This alignment not only supports higher efficiency but also enables organizations to navigate the complexities of regulatory landscapes effectively. By adopting these tools within their tech transfer framework, companies can significantly enhance their operational adeptness, ensuring that their transition from development to manufacturing is not only compliant but also seamless.
Implementing Lean Manufacturing Tools: Strategies for Waste Reduction
Lean manufacturing principles focus on improving efficiency and productivity while minimizing waste in the manufacturing process. Implementing lean tools can significantly enhance operational excellence, particularly in industries that prioritize compliance, such as pharmaceutical and food manufacturing. Among the most effective strategies are Value Stream Mapping, the 5S methodology, and the development of Standard Operating Procedures (SOP) templates.
Value Stream Mapping (VSM) is a critical tool that visualizes the flow of materials and information throughout the manufacturing process. By documenting every step involved in the workflow, organizations can identify areas of inefficiency, unnecessary steps, and potential bottlenecks. The ultimate goal of VSM is to streamline processes, creating a more efficient pathway from raw materials to finished products while simultaneously ensuring adherence to compliance regulations.
The 5S methodology—Sort, Set in order, Shine, Standardize, Sustain—provides an organized framework for workplace efficiency. By implementing these steps, manufacturers can systematically eliminate waste, maintain cleanliness, and enhance productivity. 5S fosters an environment that encourages continuous improvement, which is vital in achieving manufacturing excellence. Regular training and engagement with employees in the 5S process can lead to sustainable changes that not only comply with regulatory standards but also promote a culture of quality.
Standard Operating Procedures (SOP) are essential for ensuring consistent manufacturing practices. Well-documented SOPs provide clear, step-by-step instructions for operational processes, improving workflow and reducing variability that may lead to waste. By systematically integrating SOP templates into training programs, manufacturers can enhance employee understanding and adherence, leading to better compliance and fewer errors in production.
Incorporating these lean manufacturing tools—Value Stream Mapping, 5S methodology, and SOP templates—into manufacturing processes can result in significant waste reduction, improved efficiency, and strong compliance with industry regulations. Such strategies contribute to an organization's overall goal of achieving GMP and operational excellence.
Contamination Control: Essential Cleaning Validation and Environmental Monitoring Guides
Contamination control is critical in manufacturing settings, particularly in industries such as pharmaceuticals and biotechnology, where product safety is paramount. Effective contamination control relies heavily on properly implemented cleaning validation and robust environmental monitoring systems. Establishing thorough cleaning protocols is the first step in this direction. These protocols should outline detailed procedures for cleaning and sanitizing equipment, surfaces, and environments that come into contact with products. It is essential to ensure that these protocols are tailored to the specific processes and materials used, as different substances may require unique cleaning strategies to achieve optimal results.
Next, cleaning validation is the process of verifying that cleaning procedures effectively remove residues of products and contaminants to acceptable levels. This involves utilizing established methods to assess cleanliness, such as sampling and testing methods, to demonstrate that a given cleaning process is suitable for its intended use. Validation must be conducted initially and re-evaluated regularly, especially whenever there are changes in production processes, product formulations, or equipment. Incorporating statistical sampling techniques can enhance the efficiency of the validation process, ensuring that it is both comprehensive and manageable.
Implementing an effective environmental monitoring system is another crucial aspect of contamination control. Such systems are designed to track and evaluate the presence of microbial and particulate contamination in the manufacturing environment. Regular monitoring helps identify potential sources of contamination, allowing for timely interventions to mitigate risks. Techniques such as air sampling, surface monitoring, and personnel gowning validations form the backbone of these systems, ensuring that the facilities are maintained at compliance standards that promote product safety and overall manufacturing excellence.
Featured Resource: GMP Compliance in Pharma 4.0
The evolving landscape of the pharmaceutical industry necessitates strict adherence to Good Manufacturing Practices (GMP) while integrating modern technological advancements. One vital resource that addresses these challenges is the ebook titled "GMP Compliance in Pharma 4.0: Digitalizing Quality Systems." This comprehensive guide emphasizes the importance of digital transformation in enhancing GMP compliance and aligns closely with contemporary manufacturing processes.
The ebook outlines the key components of Pharma 4.0, including the application of data analytics, automation, and interconnected systems that support the creation of a quality-centric manufacturing environment. By embracing digitalization, organizations can streamline their operations and improve product quality, ensuring compliance with stringent regulatory requirements. The resource discusses specific technologies that facilitate real-time monitoring and control of manufacturing processes, which, in turn, can prevent deviations and promote consistent product quality.
Moreover, the ebook provides actionable insights for industry professionals looking to integrate digital tools into their GMP compliance efforts. It highlights case studies and best practices that illustrate successful implementation of digital quality systems within various organizations. Readers will discover strategies to conduct regular assessments of their processes and systems, ensuring ongoing compliance and enhancing operational efficiency.
In addition, the resource serves as a guide for pharmaceutical companies aiming to cultivate a culture of quality that aligns with today’s digital frameworks. By leveraging the knowledge and practical tools discussed in the ebook, organizations can pave the way for a more efficient manufacturing landscape while adhering to necessary compliance measures. This resource is not only pertinent for compliance officers but also for any professionals striving to foster innovation while ensuring that quality systems meet regulatory expectations.
Toolkit for Tech Transfer Project Planning: Timeline and Risk Matrix
In the realm of Good Manufacturing Practices (GMP) and efficient manufacturing, the successful execution of tech transfer projects is essential. A meticulously structured toolkit specifically designed for tech transfer project planning can facilitate this process significantly. One of the primary components of the toolkit is the project timeline, which serves as a roadmap for all activities involved in the tech transfer process.
The timeline outlines crucial milestones, deadlines, and resource allocation, providing a comprehensive view of the project’s progression. By establishing a clear timeline, project managers can ensure that each phase of the tech transfer is conducted systematically, allowing for better coordination among team members and stakeholders. Such organization not only enhances productivity but also ensures compliance with GMP standards, as it leaves little room for oversight.
Alongside the timeline, the toolkit incorporates a risk matrix, serving as an integral part of risk management in tech transfer projects. This matrix identifies potential risks associated with each phase of the project and evaluates their severity and likelihood. By categorizing risks based on their potential impact and establishing appropriate mitigation strategies, project managers can proactively address challenges before they escalate. This foresight is particularly beneficial in maintaining compliance with regulatory standards, as it enables teams to respond to unforeseen circumstances without compromising on quality or efficiency.
Ultimately, implementing a robust toolkit for tech transfer project planning empowers organizations to streamline their processes effectively, enhance their readiness to navigate challenges, and align their operations with GMP principles. By ensuring precise planning through timelines and risk matrices, companies can foster an environment of manufacturing excellence while adhering to regulatory requirements.
Molgenium – Empowering Pharma Excellence Through Knowledge.
© Molgenium 2025. All rights reserved.